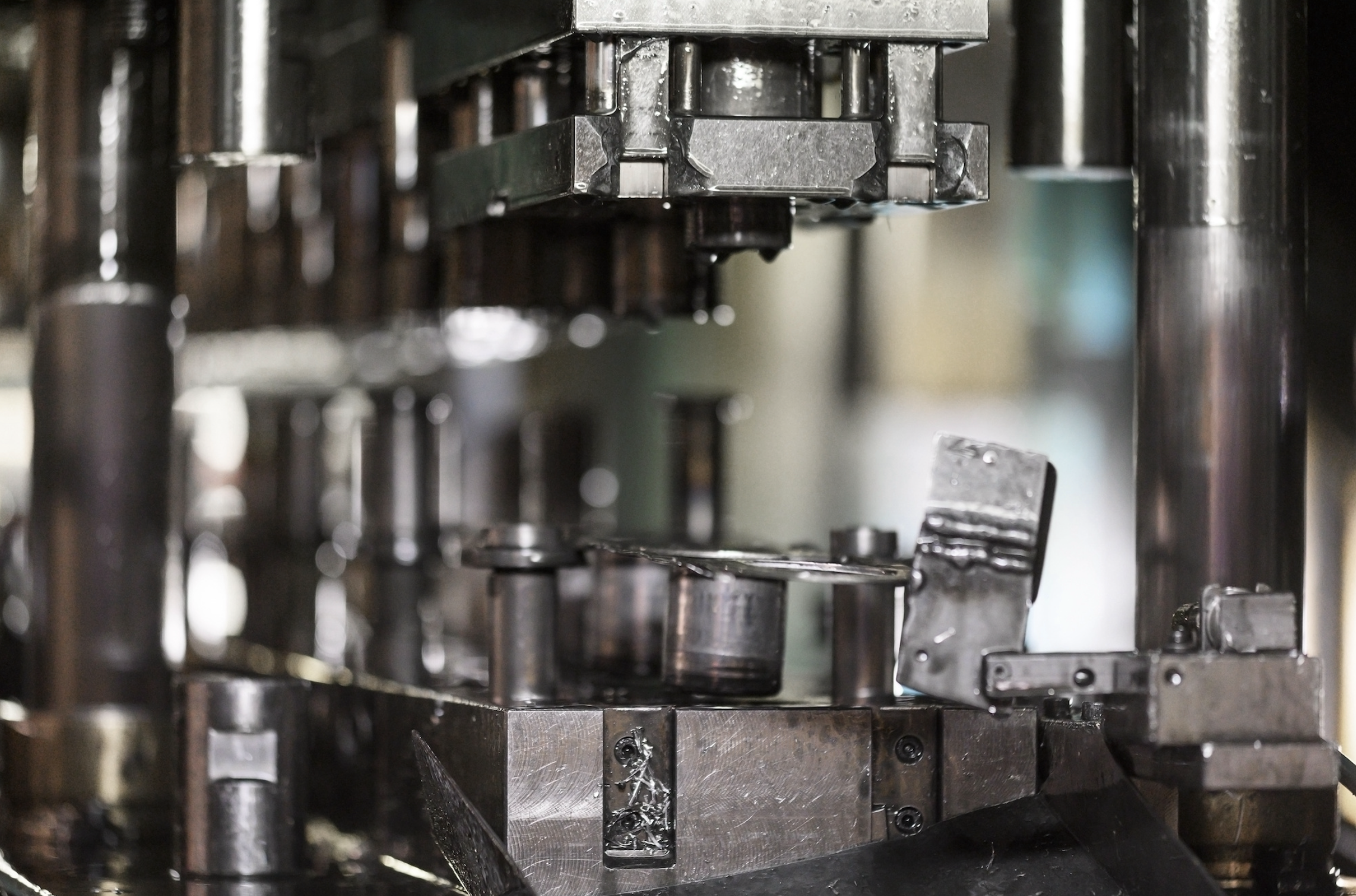
Metal Stamping
Quality • On-time delivery
responsiveness • flexibility
At Pentar Stamping our goal is to give our customers high-quality precision metal stamping no matter what the size or annual volume. Our determination to provide high-quality metal stamping begins with the development of the product and doesn’t end until it is delivered to your door. Every member of our staff has been trained to ensure that quality metal stamping is being produced throughout the entire process. We are focused on working with you to create an economical product with consistent and lasting quality.
Automotive
Industrial
Agriculture
RVs
Electrical
Air Craft
Motorcycles
ATVS
Automotive Industrial Agriculture RVs Electrical Air Craft Motorcycles ATVS
What we offer
Press Equipment
80 Ton Gap Frame Press – 39.4 x 23.6 x 10.65-13.8 – 5.12 Stroke
160 Ton – 49.21 x 29.92 – 7.87 Stroke
200 Ton Gap Frame Press – 95.2 x 33.4 x 14.9-19.6 – 9.84 Stroke
200 Ton Straight Side Press – 95.2 x 33.4 x 14.8-19.6 – 9.84 Stroke
300 Ton Straight Side Press – 120 x 50 x 24.0-36.0 – 16.0 Stroke
400 Ton Straight Side Press – 108 x 60 x 36.0-12.0 – 17.0 Stroke
Capabilities
Stamping Presses up to 400 tons
Stamping Thickness 0.01-0.2″
Tolerance: +/- .005
Tonnage: Up to 400 Tons
Pieces Per Year: 25-15,000,000
Materials: Hot Roll, Cold Roll, Stainless Steel, Aluminum, Copper, Galvanized Steel, and Spring Steel
Quality: PPAP, APQP, PFMEA, Hardness Testing, & Destructive
Less than 5 parts Per Million Defective
100% On-Time Delivery
Operations
Bending – the material is deformed or bent along a straight line.
Flanging – the material is bent along a curved line.
Embossing – the material is stretched into a shallow depression. Used primarily for adding decorative patterns.
Blanking – a piece is cut out of a sheet of the material, usually to make a blank for further processing.
Coining – a pattern that is compressed or squeezed into the material. Traditionally used to make coins.
Drawing – the surface area of a blank is stretched into an alternate shape via controlled material flow.
Stretching – the surface area of a blank is increased by tension, with no inward movement of the blank edge. Often used to make smooth auto-body parts.
Ironing – the material is squeezed and reduced in thickness along a vertical wall. Used for beverage cans and ammunition cartridge cases.
Reducing/Necking – used to gradually reduce the diameter of the open end of a vessel or tube.
Curling – deforming material into a tubular profile. Door hinges are a common example.
Hemming – folding an edge over onto itself to add thickness. The edges of automobile doors are usually hemmed.
Secondary Services:
In-House Welding and Assembly
In-House Tool Room
E-Coat, Powder Coat, Autophoretic Coating
High-Volume Production Stamping
High-Volume Production Stamping
Stamping parts over 1,000,000 units per year is no problem for Pentar. A large part of our core business is high-volume stampings that we ship out daily to our customers.
Aftermarket stamping
Looking for a supplier to manufacture a part that is no longer in full production? Pentar Stamping is experienced with these types of challenges and is willing to take on complex aftermarket service work. We will work with you to establish your exact needs, part specifications, and part tolerances based on your existing tooling and economic considerations in order to reach the desired level of quality necessary for replacement or service parts.
low-volume stamping
We excel at expediting low-volume production runs utilizing your existing tooling. Low-volume metal stamping often falls outside the core competencies of large manufacturers, but that is not the case with Pentar. We have established procedures that help run parts quickly and efficiently to save you money. We work in conjunction with your company to develop a plan that is mutually beneficial, and economical keeping the higher costs associated with low-volume production to a minimum.
emergency stamping
Emergency issues resulting in a slowdown or loss of production can be devastating, not to mention frustrating and stressful. Pentar Stamping can be at your service 24 hours a day, 7 days a week. If you encounter production issues for whatever reason, we can be there to help you get up and running again. Contact us to discuss your emergency metal stamping project and we will use our experienced team to process your order as quickly and economically as possible without sacrificing quality.
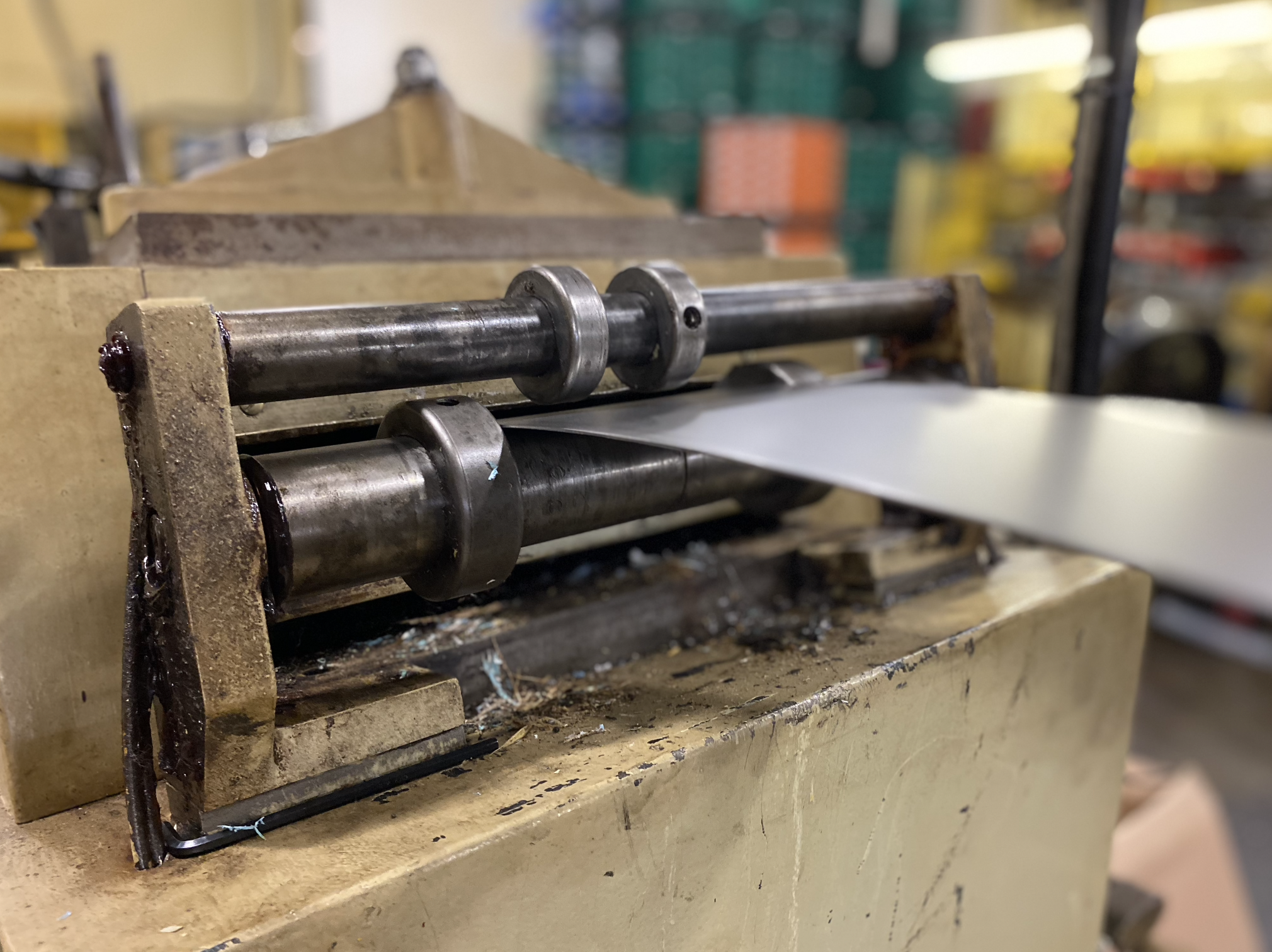
Our GOAL is your success
Our team is experienced in manufacturing precision metal stampings for both long and short-production, as well as emergency work. Our knowledge gained from years of completing emergency production runs and taking over work from existing production means that we know what complications can arise throughout the processes and life of a product. We have been successful in avoiding many of these complications by utilizing long-term knowledge and dedication to quality.